At Leto Golf Apparel Manufacturing, ensuring high-quality manufacturing and consistency in our OEM (Original Equipment Manufacturer) services is paramount. This article delves into the rigorous quality control processes, consistent communication, collaboration, and continuous improvement strategies that we employ to achieve this.
- Rigorous Quality Control Processes
- Material Sourcing and Inspection
- State-of-the-Art Manufacturing Facilities
- Standardized Production Procedures
- In-Process Quality Checks
- Final Quality Inspection
- Consistent Communication and Collaboration
- Client Collaboration
- Transparent Reporting
- Continuous Improvement
- Feedback Loop
- Training and Development
- Conclusion
- FAQs
Material Sourcing and Inspection
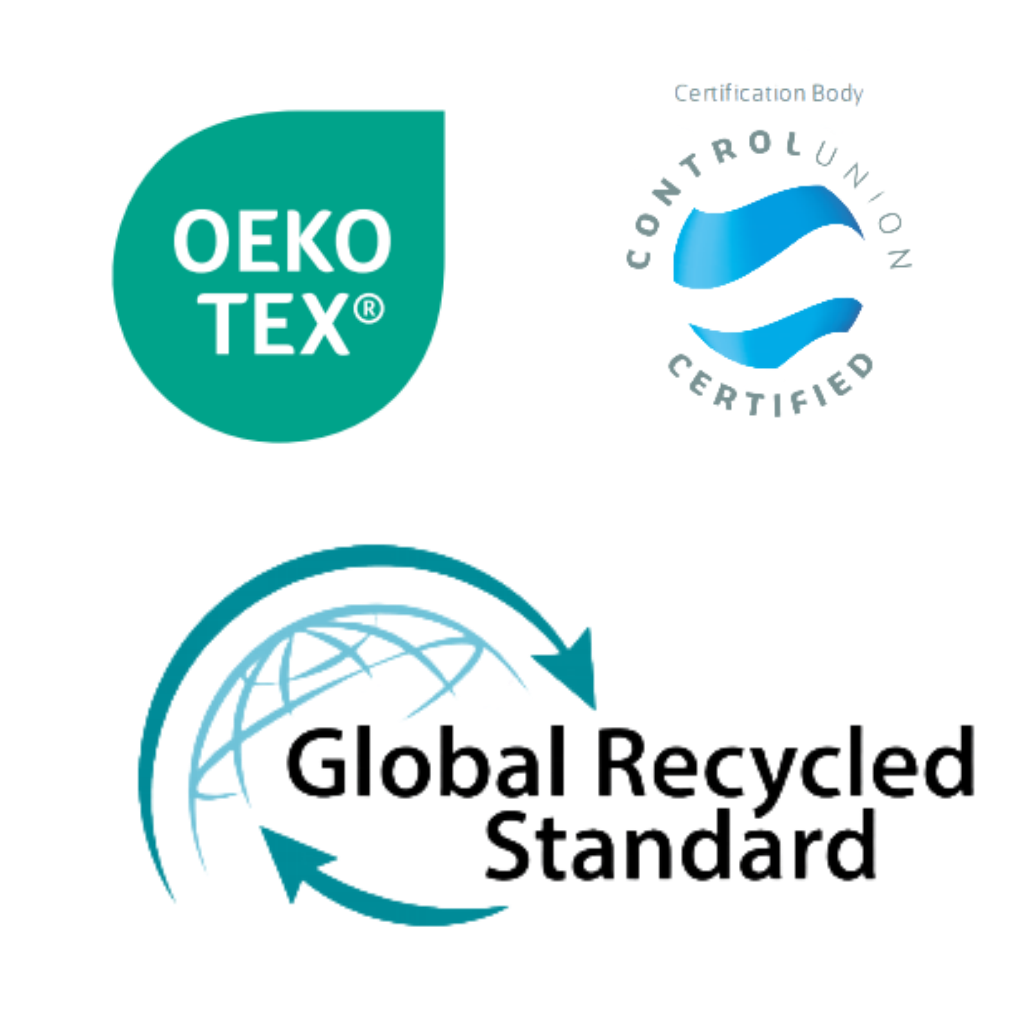
Premium Suppliers: We partner with reputable suppliers to source high-quality materials. Every batch of fabric and accessories is carefully inspected upon arrival to ensure they meet our stringent standards.
Material Testing: We conduct various tests on materials for durability, colorfastness, shrinkage, and breathability to ensure they are suitable for golf apparel.
Advanced Machinery: Our manufacturing facilities are equipped with the latest technology and machinery, allowing for precise and efficient production processes.
Skilled Workforce: We employ a team of highly skilled and experienced workers trained in the best practices of garment manufacturing.
Standardized Production Procedures
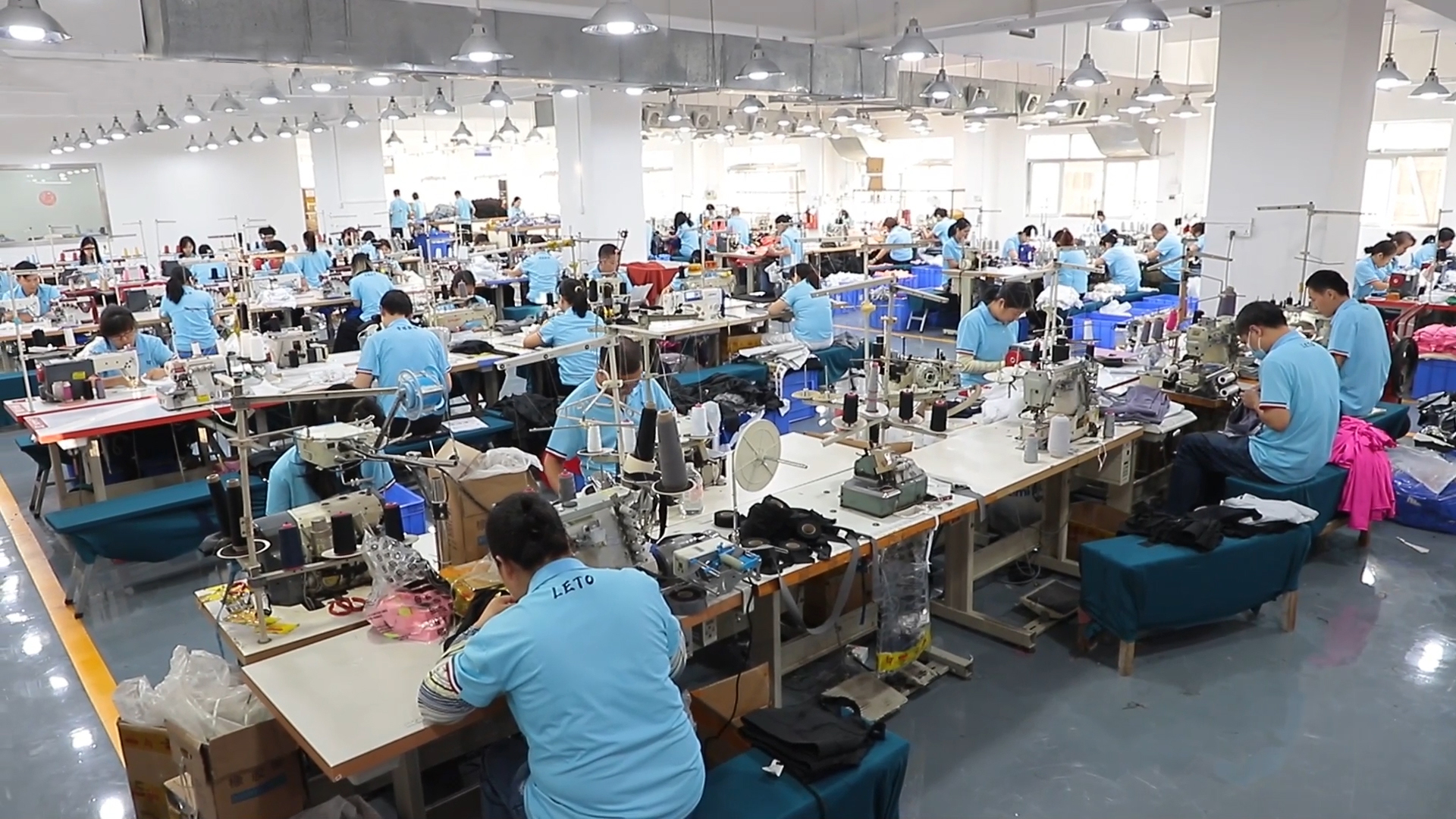
Detailed Specifications: We work closely with clients to develop detailed production specifications, including patterns, measurements, and finishing details. This ensures that every piece produced matches the client’s exact requirements.
Production Manuals: We create comprehensive production manuals for each order, outlining every step of the manufacturing process. This helps maintain consistency and quality across all production runs.
Multiple Checkpoints: Quality checks are performed at multiple stages throughout the production process, from cutting and sewing to finishing and packing. This helps identify and address any issues early on.
Sample Review: Initial samples are reviewed and approved by both our internal quality control team and the client before full-scale production begins.
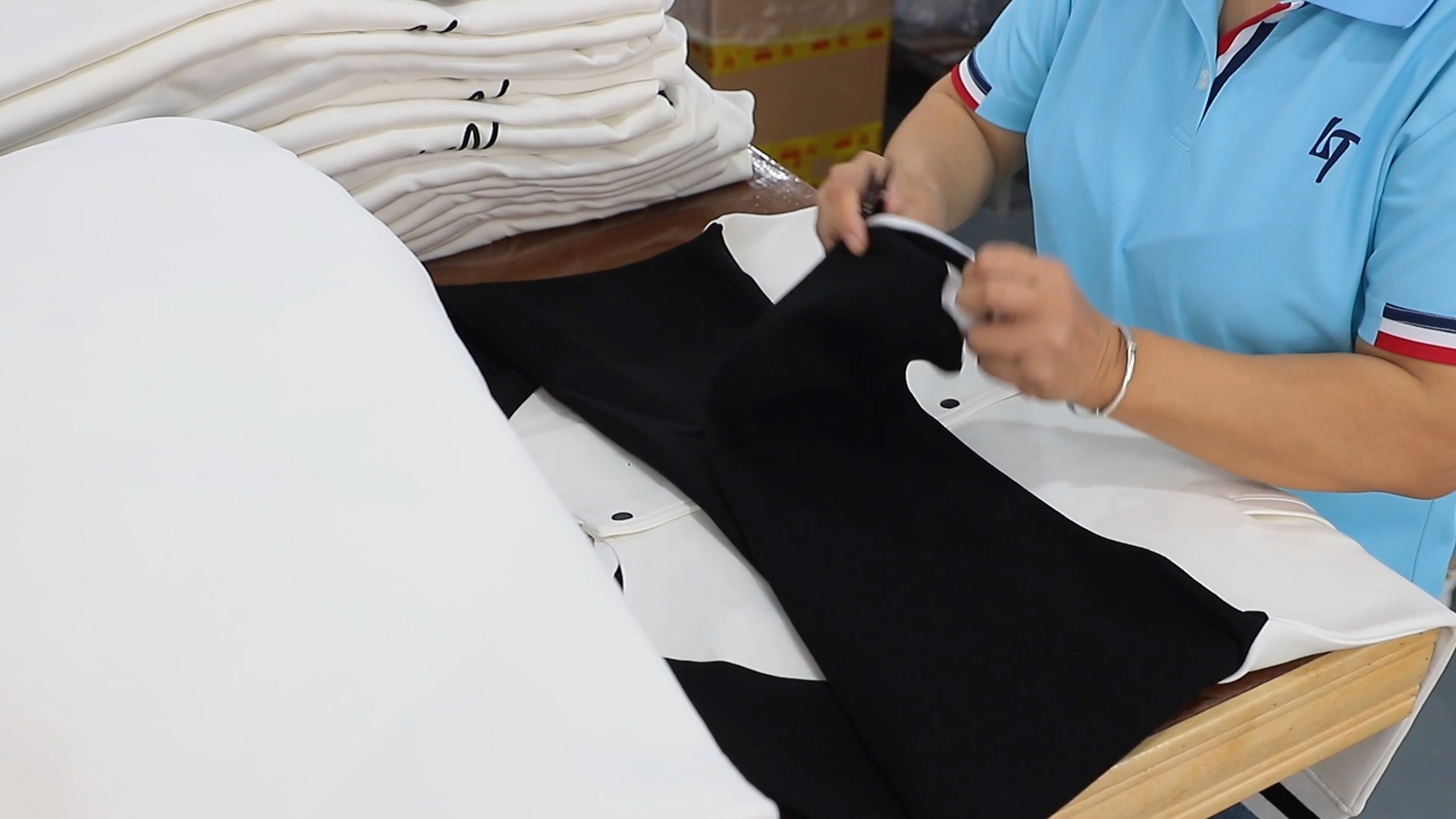
Comprehensive Inspections: Each finished garment undergoes a thorough final inspection to check for defects, proper fit, and adherence to design specifications.
Batch Testing: Random batch testing is conducted to ensure overall consistency and quality across the entire production run.
Consistent Communication and Collaboration
Design Consultations: We maintain open lines of communication with clients throughout the design and production process to ensure their vision is accurately translated into the final product.
Approval Stages: Clients are involved in key approval stages, including prototype review and final sample approval, to ensure their satisfaction.
Regular Updates: We provide regular updates to clients on the status of their orders, including any potential issues and proposed solutions.
Detailed Reports: Post-production reports detail the entire manufacturing process, including quality control measures and final inspection results.
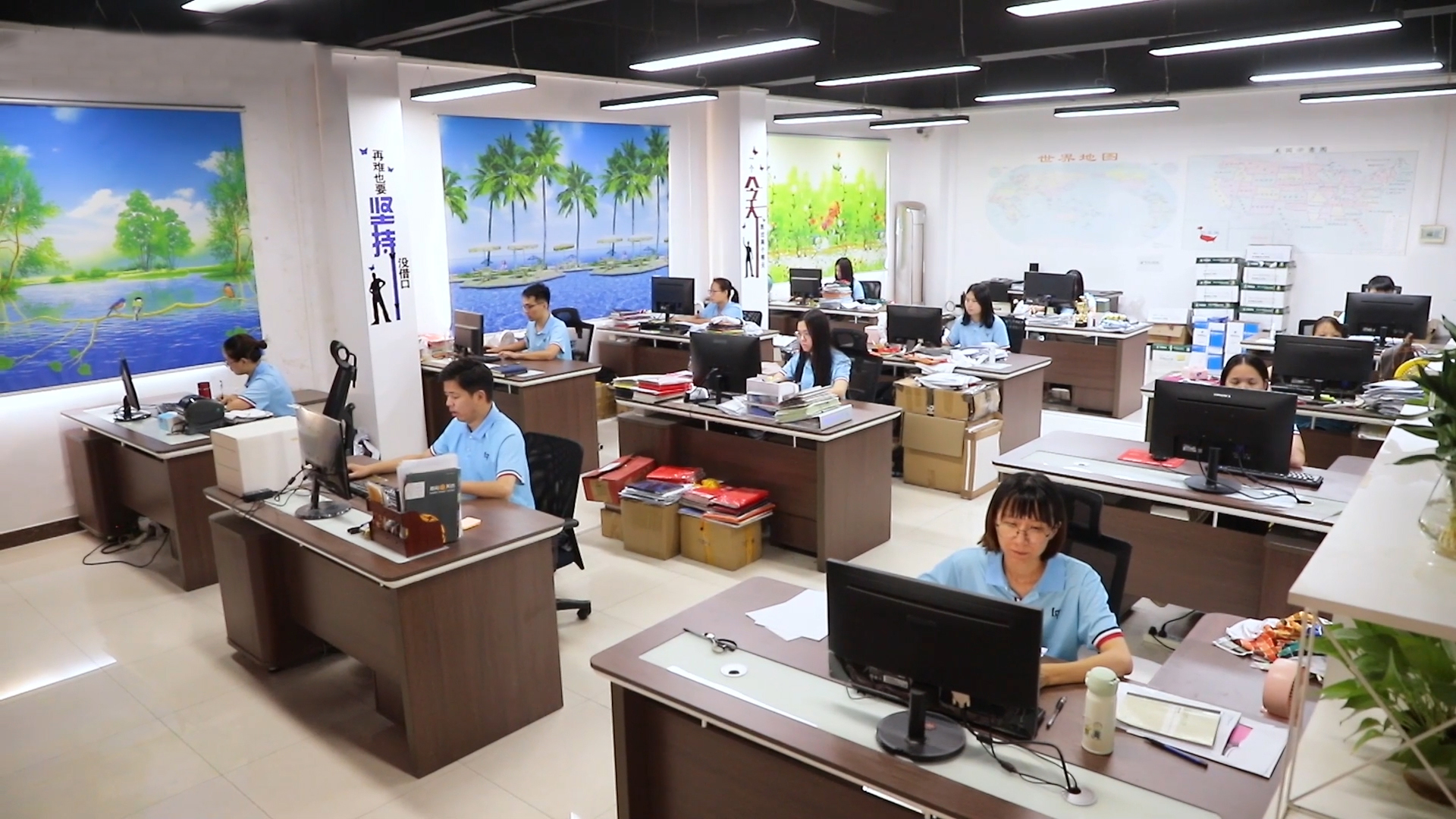
Client Feedback: We actively seek and value feedback from our clients to continuously improve our services and processes.
Internal Reviews: Regular internal reviews and audits help us identify areas for improvement and implement best practices in quality control and production efficiency.
Training and Development
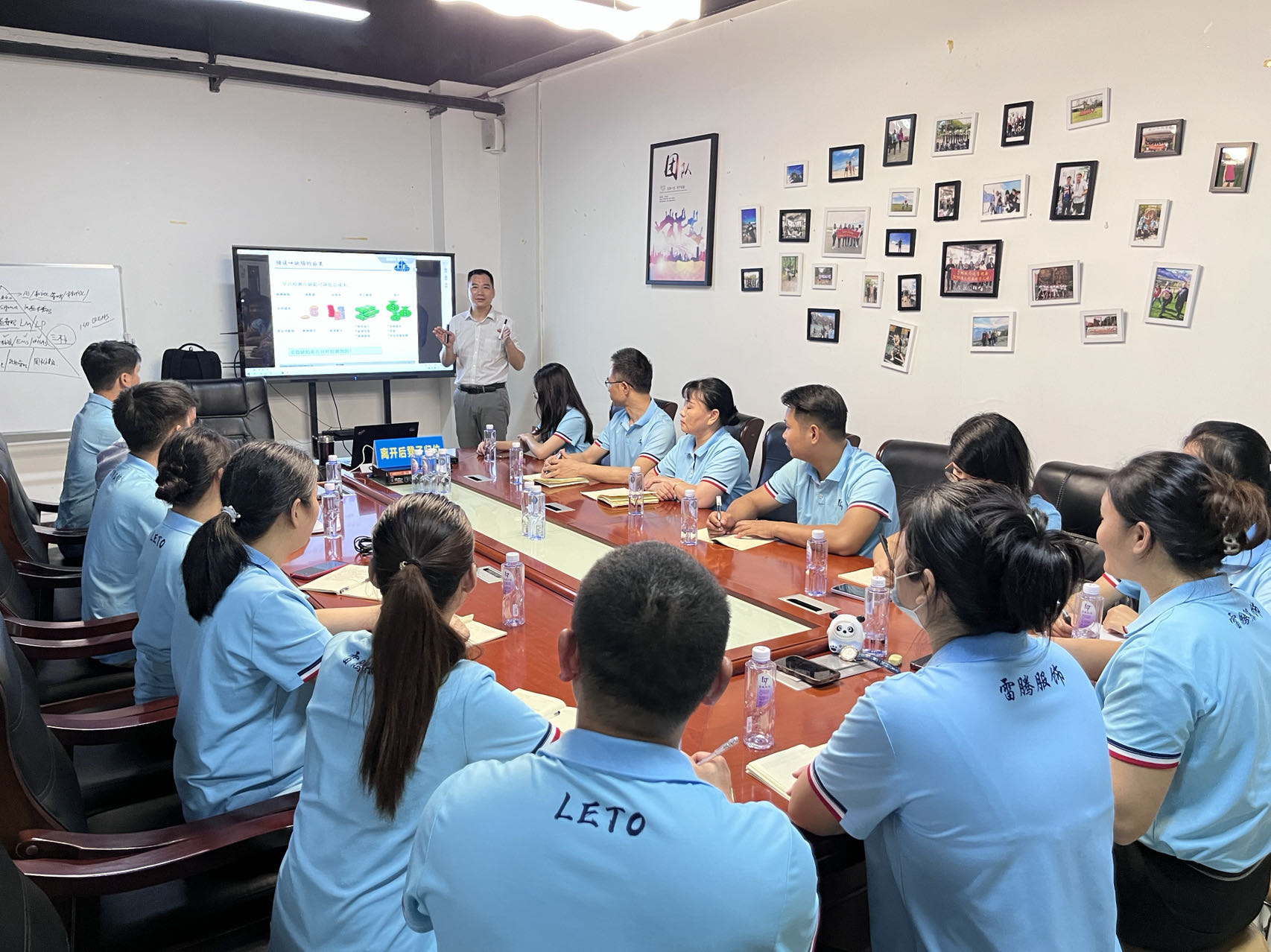
Ongoing Training: Our workforce undergoes regular training to stay updated on the latest manufacturing techniques and quality control standards.
Process Optimization: We continuously invest in process optimization and technology upgrades to enhance our manufacturing capabilities and maintain high standards of quality and consistency.
At Leto Golf Apparel Manufacturing, our commitment to quality and consistency is unwavering. By employing rigorous quality control processes, maintaining consistent communication and collaboration with clients, and continuously seeking ways to improve, we ensure that every piece of golf apparel we produce meets the highest standards of excellence. Whether you are a startup or an established brand, our OEM services are designed to deliver superior products that align with your vision and exceed your expectations.
We focus on material sourcing and inspection, state-of-the-art manufacturing facilities, standardized production procedures, in-process quality checks, and final quality inspections.
We maintain open communication with clients, involve them in key approval stages, and provide regular updates and detailed reports.
We actively seek client feedback, conduct regular internal reviews, invest in ongoing training for our workforce, and optimize our processes and technology.