Final Product Inspection: Thorough examination of finished garments for any defects or inconsistencies.
Standardized Operating Procedures (SOPs)
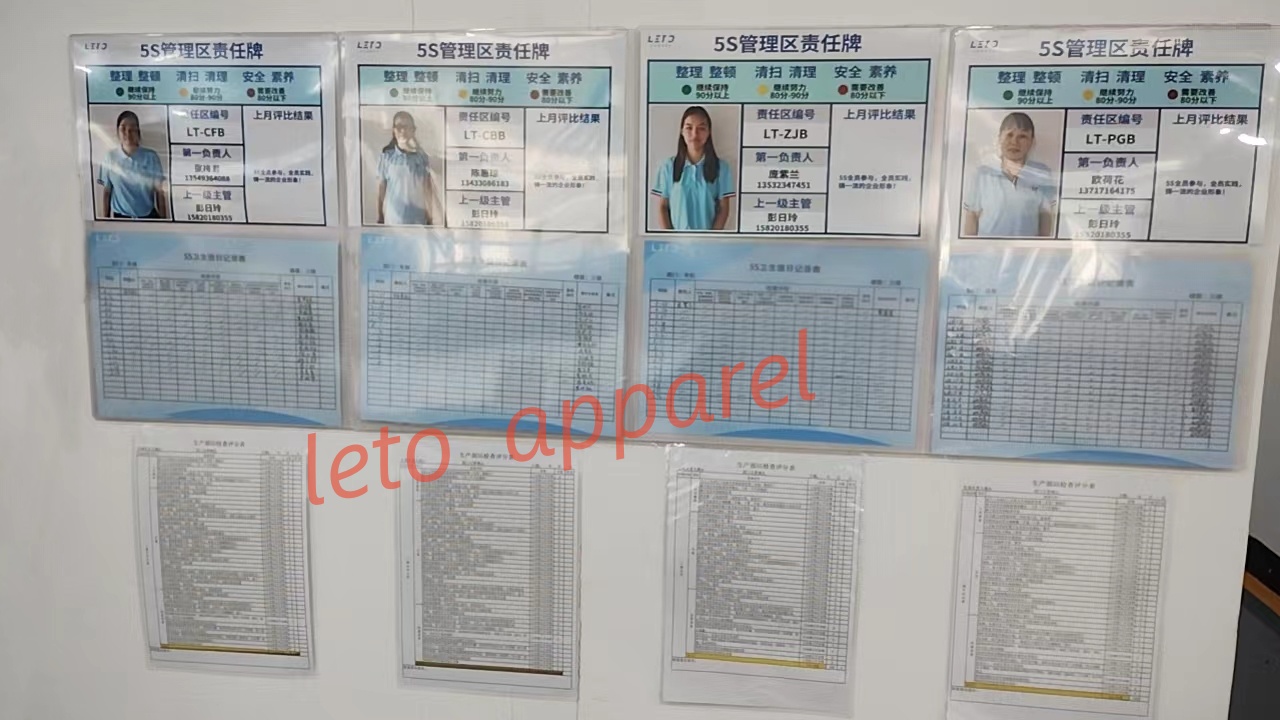
We develop and follow detailed Standard Operating Procedures (SOPs) for every step of the production process. These SOPs ensure that each task is performed consistently and accurately, regardless of who performs it.
SOP Components:
- Detailed Instructions: Clear, step-by-step guidelines for each production task.
- Quality Benchmarks: Specific criteria that each product must meet to pass inspection.
- Documentation: Comprehensive records of production processes and quality checks for accountability and traceability.
We value our clients' feedback and use it to continually improve our processes. By maintaining open lines of communication, we ensure that we understand and meet our clients' evolving needs and expectations.
Feedback Implementation:
- Regular Surveys: Collect feedback from clients to identify areas for improvement.
- Performance Reviews: Analyze feedback to enhance production techniques and quality control measures.
- Client Collaboration: Work closely with clients to tailor our processes to their specific requirements.
Environmental and Social Responsibility
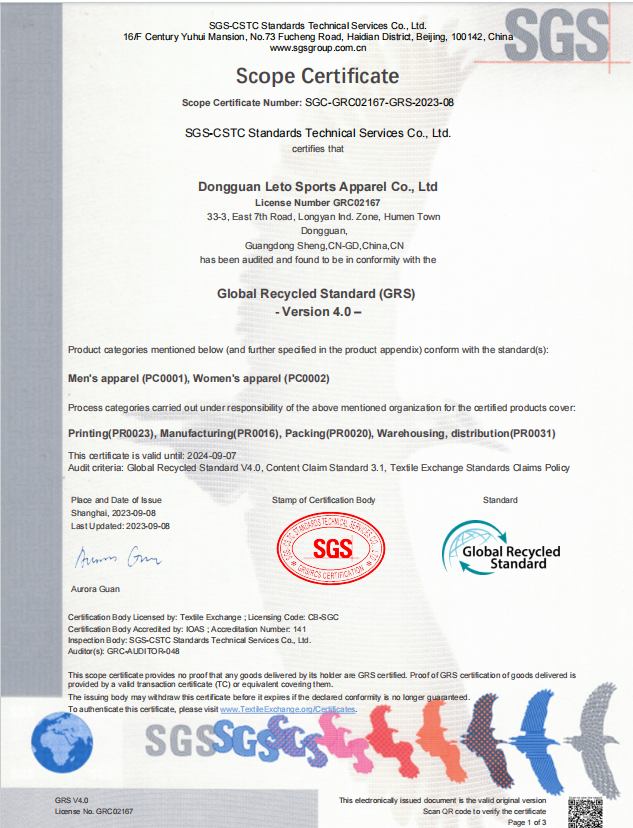
We are committed to sustainable and ethical production practices. By adhering to environmental standards and ensuring fair labor practices, we not only produce high-quality garments but also contribute positively to the community and the environment.
Sustainable Practices:
- Eco-Friendly Materials: Sourcing materials that are environmentally friendly and sustainable.
- Waste Reduction: Implementing practices to minimize waste and promote recycling.
- Fair Labor: Ensuring fair wages and safe working conditions for all employees.
Conclusion: Committing to Quality and Responsibility
At Leto Golf Apparel Factory, our meticulous approach to quality control, combined with advanced technology and skilled craftsmanship, ensures that every garment we produce meets the highest standards. By continually refining our processes and embracing feedback, we strive to exceed our clients' expectations and deliver exceptional value.
For more information about our quality control processes or to discuss your production needs, please contact us. Partner with Leto and experience the difference of working with a factory that prioritizes quality and customer satisfaction at every step.
We conduct thorough inspections of all fabrics and materials upon arrival to ensure they meet our quality and consistency standards.
What technologies do you use to maintain quality control?
We use automated cutting machines, computerized sewing machines, and quality inspection software to ensure precision and consistency in our production processes.
We collect feedback through regular surveys and performance reviews, which help us identify areas for improvement and tailor our processes to meet our clients' needs.