At Leto Golf Apparel Factory, we understand that maintaining consistent quality throughout the entire supply chain—from raw materials to finished products—is crucial for producing high-performance golf apparel. Our comprehensive quality assurance system is designed to monitor and control every phase of the production process, ensuring that each garment meets our rigorous standards. Here’s how we achieve consistent quality across our supply chain:
The foundation of a high-quality product lies in the materials used. We partner with trusted suppliers who provide premium fabrics and accessories that meet our stringent quality criteria.
We choose suppliers with a proven track record of providing high-quality materials.
Certification and Compliance
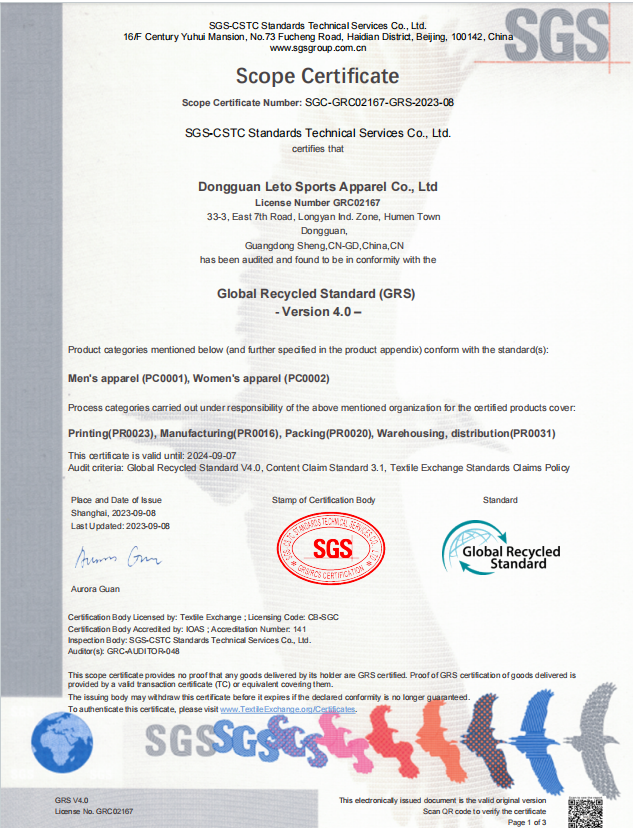
Suppliers must adhere to international quality standards and certifications, such as OEKO-TEX and GOTS.
Conduct periodic audits and evaluations of supplier facilities to ensure ongoing compliance with our quality standards.
Inspect raw materials upon arrival for defects, consistency, and adherence to specifications.
Conduct laboratory tests to verify material properties like tensile strength, colorfastness, and breathability.
Approve material samples before bulk orders to ensure they meet our quality requirements.
Our production processes are designed to ensure precision and consistency, minimizing the risk of errors and defects.
Utilize advanced automated machinery for cutting, stitching, and finishing to ensure accuracy and uniformity.
Regular Maintenance
Perform regular maintenance and calibration of equipment to maintain peak performance.
Provide ongoing training to our technicians and seamstresses to keep them updated on the latest techniques and quality standards.
Standard Operating Procedures (SOPs)
Implement detailed SOPs for every production task to ensure consistency and quality.
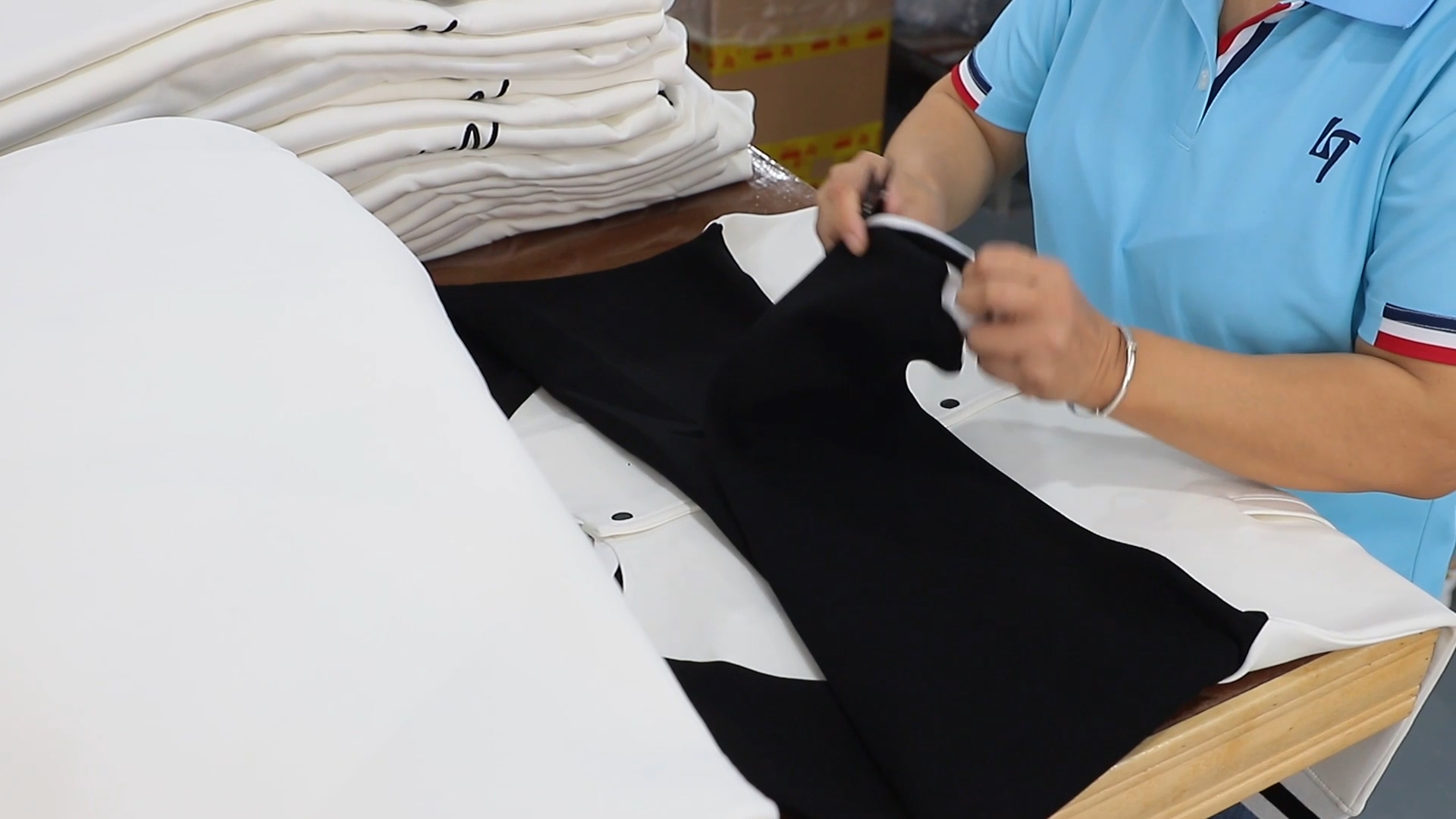
We conduct rigorous quality control checks at every stage of production to identify and address any issues promptly.
Verify the setup and calibration of machinery before starting production.
Conduct regular inspections during production to monitor for defects and ensure adherence to design specifications.
Perform thorough inspections of finished products to ensure they meet our quality standards.
Conduct visual inspections to check for defects such as uneven stitching, color discrepancies, and fabric flaws.
Perform functional tests to verify the performance of the garment, such as stretchability, wear resistance, and breathability.
Comprehensive Documentation and Traceability
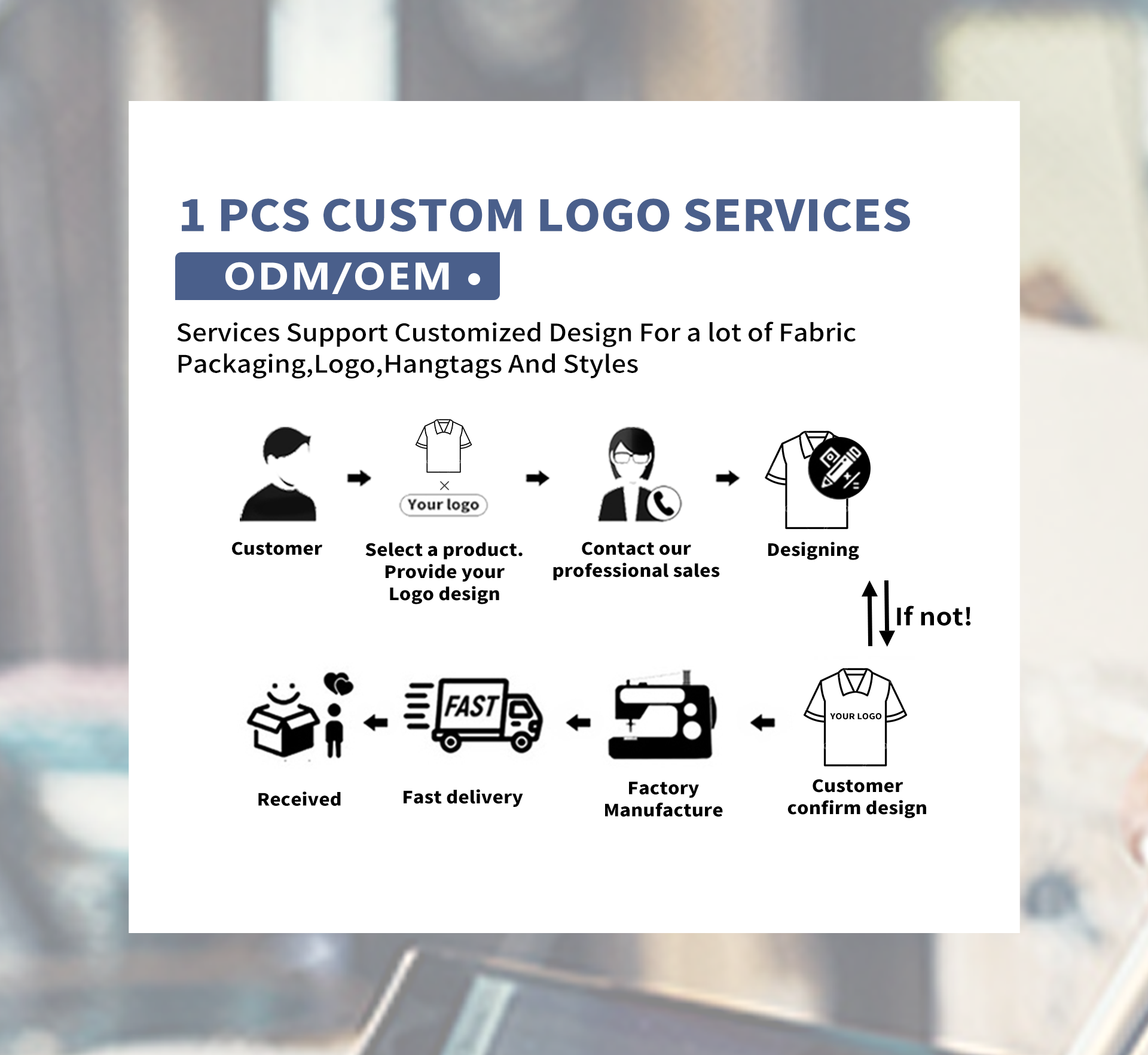
Maintaining detailed records and traceability throughout the supply chain helps us monitor quality and quickly address any issues that arise.
Keep detailed records of each production batch, including raw material sources, production dates, and inspection results.
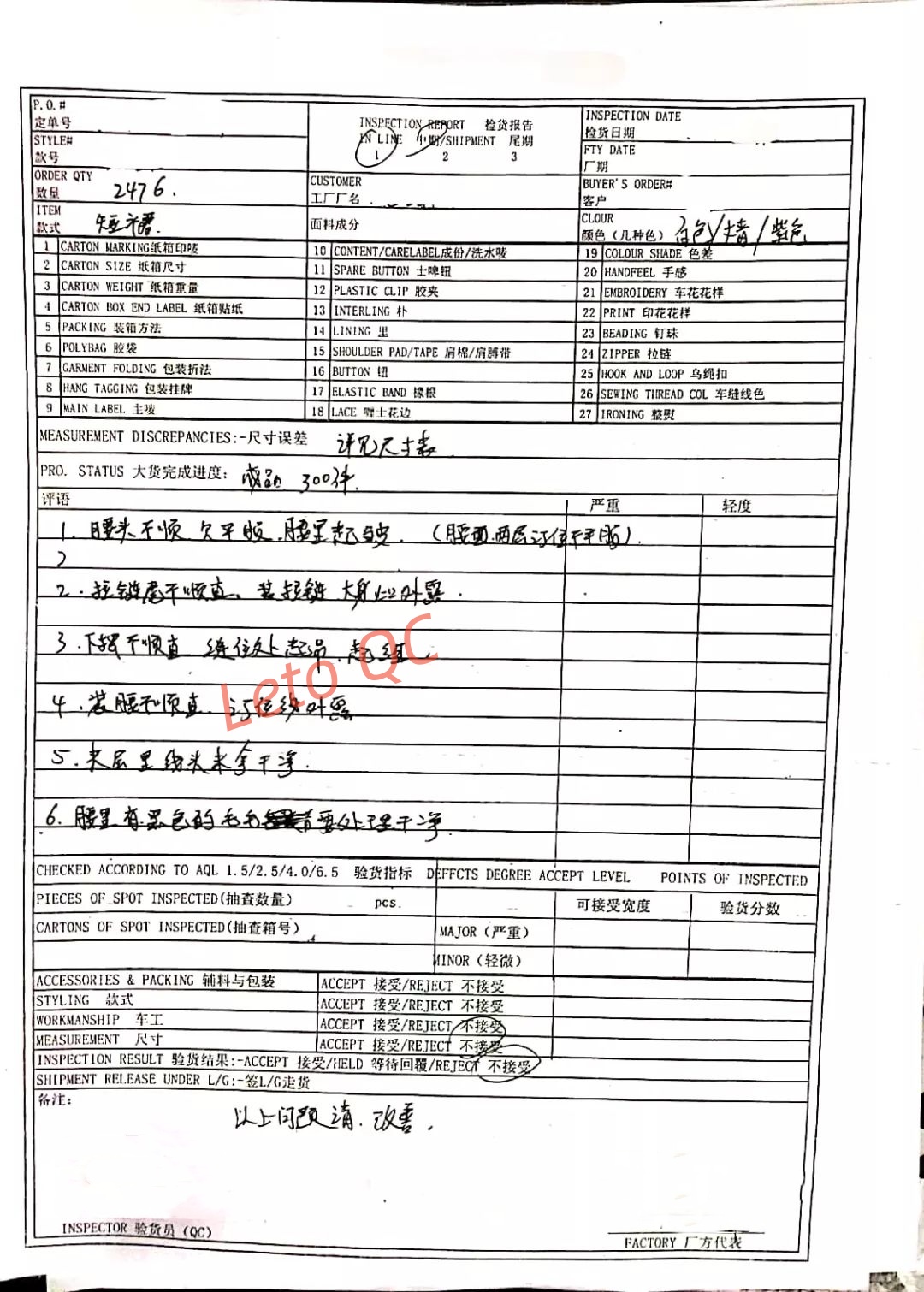
Generate comprehensive quality reports that document inspection findings and corrective actions taken.
Implement a robust tracking system to trace raw materials from suppliers to finished products.
Use unique product IDs and barcodes to track finished garments through the supply chain and distribution.
Customer Feedback and Continuous Improvement
We value our clients’ feedback and use it to continually improve our processes and products.
Regularly survey clients to gather feedback on product quality and performance.
Analyze feedback to identify areas for improvement and implement necessary changes.
Work closely with clients to understand their needs and tailor our processes to meet their specific requirements.
Conduct regular internal quality audits to assess and improve our processes.
Training and Development
Invest in continuous training and development programs for our staff to enhance their skills and knowledge.
At Leto Golf Apparel Factory, ensuring consistent quality across our supply chain is a top priority. By sourcing high-quality raw materials, streamlining production processes, implementing rigorous in-process quality control, maintaining comprehensive documentation, and continuously seeking customer feedback, we are able to produce golf apparel that meets the highest standards of durability, comfort, and performance.
For more information about our quality assurance practices or to discuss your production needs, please contact us. Partner with Leto and experience the difference of working with a factory that is committed to excellence at every step.
Suppliers must adhere to international quality standards and certifications, such as OEKO-TEX and GOTS.
We conduct initial screenings, lab tests, and sample approvals to ensure that raw materials meet our quality requirements.
We conduct regular internal quality audits and invest in continuous training and development programs for our staff.